Der lange Weg eines Leuchtstiftes
23.9.2012, 13:36 Uhr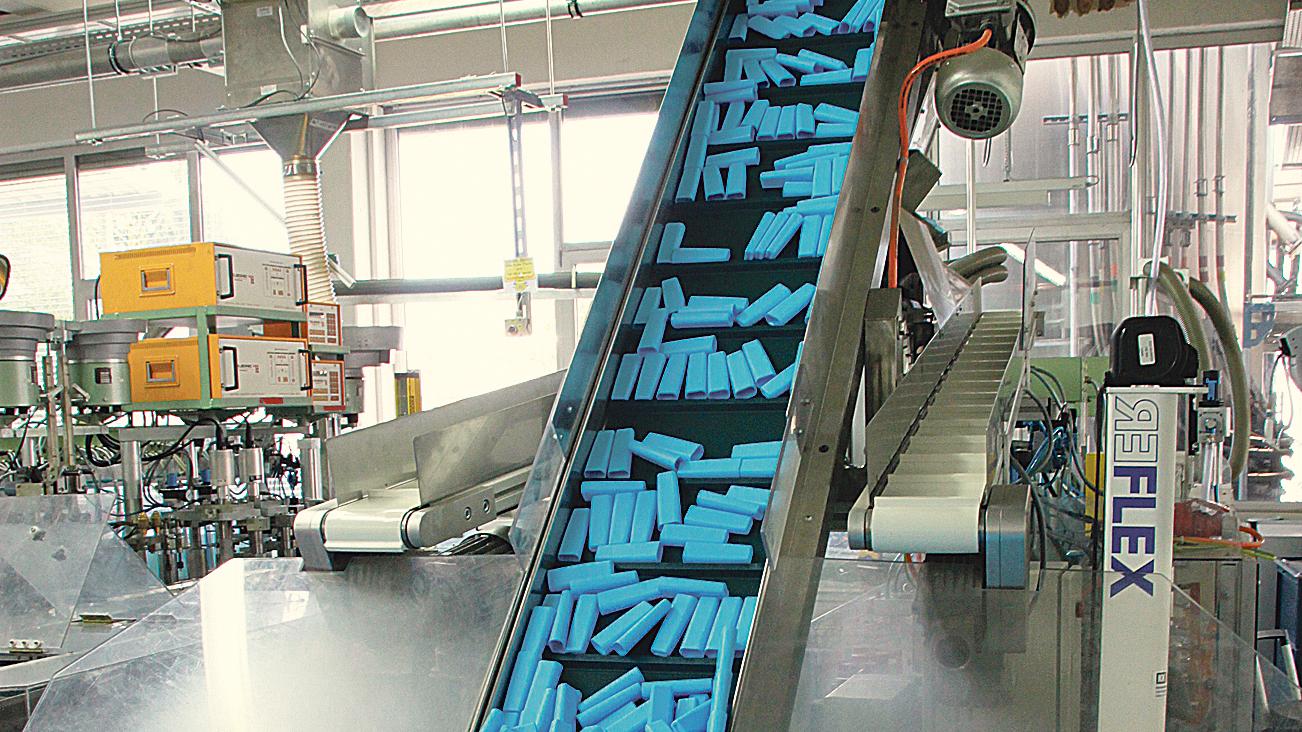
700 Meter. So viel hat ein Boss-Stift in der Vergangenheit im Schwan-Stabilo-Werk Weißenburg vom Materialdepot zurückgelegt, bis er fertig verpackt im Hochregallager landete. Unbefriedigend, befand Thomas Hildenbrand. Er ist seit fünf Jahren beim Stiftehersteller beschäftigt und leitet die Abteilung Fraktal Produktion. Dort kümmert er sich um „moderne Fertigungsstrukturen“, wie er seine Tätigkeit selbst beschreibt.
Das Boss-Projekt in Weißenburg ist inzwischen abgeschlossen. Aus 700 Metern Wegstrecke sind 410 geworden. Einsparung insgesamt: 600 000 Euro im Jahr. Das liegt natürlich nicht nur an den dichter zusammenliegenden Produktionsschritten, sondern an mehreren Faktoren, betont Hildenbrand. „Unser Ziel war es, das Produkt möglichst nicht mehr aus der Hand zu legen, bis es fertig für die
Verpackung ist.“ Zwischenlager wurden aufgelöst. „Wir haben einfache, selbstregulierende Nachfüllkreise geschaffen“, beschreibt es der Produktionsoptimierer.
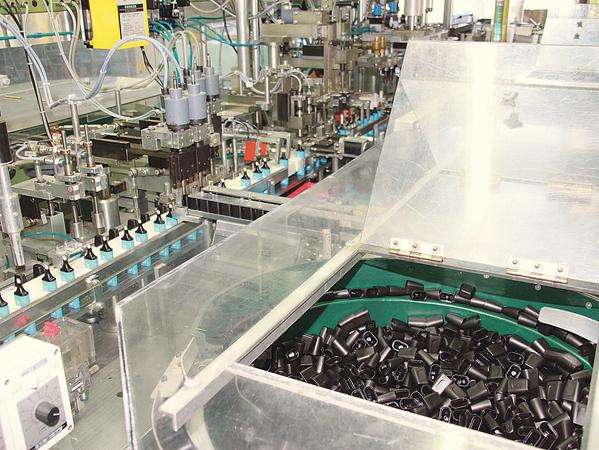
Hildenbrand kommt aus der Automobilbranche, der Vorzeigeindustrie in Deutschland in Sachen Effizienz. Die Autobauer waren die ersten, die erkannt haben, wie teuer sie ihre Lager kommen. „Just in Time“ hieß die Lösung. Die Zulieferer müssen nun pünktlich mit dem Nachschub anrücken, damit die Bänder nicht stillstehen. Das Lager rollt täglich quer über die deutschen Straßen.
Individuelle Lösungen
Die Problematik bei einem kleinen und weniger komplexen Produkt wie dem Stabilo-Boss ist freilich anders gelagert. Hildenbrand: „Die Lösungen sind immer produktspezifisch. Das muss man unterschiedlich handhaben, ob man bei einem in sehr großer Stückzahl produziertes Produkt Potenziale heben will oder bei einem in kleiner Stückzahl.“
Im Weißenburger Werk des Stifteherstellers Schwan-Stabilo taten sich Möglichkeiten einer Optimierung auf, als die Cosmetics-Sparte vor knapp vier Jahren eine neue Halle bekam. Dadurch wurden Flächen frei, auf denen Hildenbrand zusammen mit den Beschäftigten die neue Boss-Fabrikation realisieren konnte: mit den alten Maschinen – und bei fast 1 000 Quadratmeter weniger Platzbedarf. „Errechnet hatten wir ursprünglich eine Einsparung von 300 Quadratmetern“, blickt der Abteilungsleiter zurück. Doch weil die Zwischenlager überflüssig wurden, gab es weitere freie Flächen.
„Jetzt haben wir die einzelnen Arbeitsschritte möglichst nah beieinander“, stellt Thomas Hildenbrand fest. Zufrieden ist er deshalb aber nicht. „Wir haben noch keinen fertigen Zustand erreicht.“ Den gibt es genau genommen gar nicht. Stückzahlen ändern sich, neue Artikel kommen hinzu, die Produktion will ständig angepasst werden. Hildenbrand hat bereits den nächsten Schritt im Kopf. Sobald die neue Kantine (wir berichteten) fertig ist, will er die Anlieferung des Materials und die Abholung der fertigen Stifte effizienter machen. „Wir haben jetzt schon die Transportzeit um 20 bis 30 Prozent reduziert“, sagt er. Doch das soll noch nicht das Ende der Fahnenstange sein.
65 Millionen Boss-Marker stellt Schwan-Stabilo jedes Jahr in den verschiedensten Farben in Weißenburg her. Die verbesserte Effizienz ermöglicht eine Produktion beinahe auf Zuruf. Das hat den Warenbestand im Weißenburger Hochregallager an der Augsburger Straße um fast ein Viertel reduziert. Auch das hilft sparen. Die Faustformel lautet, dass eingelagerte Waren pro Jahr etwa ein Viertel ihres Wertes an Kosten verursachen. Und das flexible Reagieren auf eingehende Bestellungen ist noch aus einem anderen Grund geboten. Auch die Einzelhändler haben die Möglichkeit erkannt, ihre Lagerkosten zu senken: Sie bestellen heute kurzfristiger, in kleineren Mengen und erwarten eine schnellere Lieferung.
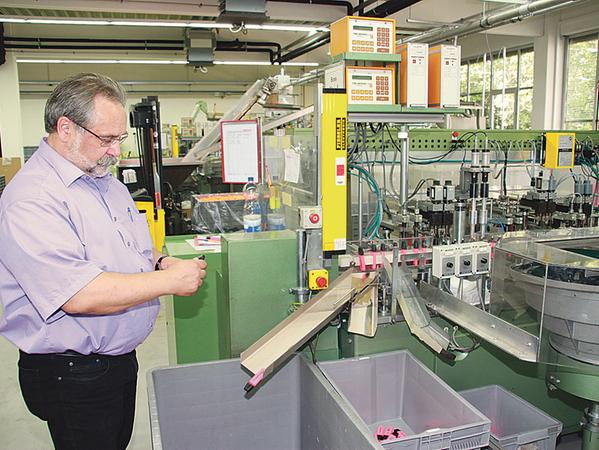
Die durch die komprimierte Boss-Produktion frei gewordenen Flächen in den Hallen zwischen Augsburger Straße und Industriestraße dienen dazu, auch Artikel in kleineren Stückzahlen im Weißenburger Werk herstellen zu können. Teile der Produktion hat Schwan-Stabilo von Tschechien zurück nach Weißenburg geholt. Das hiesige Werk ist nämlich der Spezialist für alle Stifte auf Tintenbasis innerhalb des Stabilo-Konzerns. Hildenbrand: „Wir haben letztlich eine höhere Produktvielfalt bei gleicher Mitarbeiterzahl.“
Denn Schwan-Stabilo hat die verbesserte Effizienz nicht zum Anlass genommen, um Personal abzubauen. Die frei gewordene Zeit nutzt der Stiftehersteller zum einen für die neuen Produkte und zum anderen für Schulungen. „Dadurch laufen dann wiederum die Maschinen stabiler“, ist Thomas Hildenbrand überzeugt. Auch das ist eine Möglichkeit, um in Hochlohnländern wie Deutschland die Produktion zu optimieren.
Keine Kommentare
Um selbst einen Kommentar abgeben zu können, müssen Sie sich einloggen oder sich zuvor registrieren.
0/1000 Zeichen